Adopting Maintenance 4.0 means placing data intelligence at the heart of your maintenance operations. Through the Internet of Things (IoT) and Artificial Intelligence (AI), businesses can predict, prevent and optimise interventions. However, this shift is not without its challenges. From change management to data security, discover how to tackle these issues in a proactive and structured manner.
Key challenges in transitioning to maintenance 4.0
To ensure a smooth transition, it’s essential to identify the most common obstacles and address them strategically.
1. Engaging teams to embrace change
Maintenance 4.0 requires a rethinking of traditional processes, which may cause apprehension among team members. Involving employees from management to operations early on is necessary.
To foster support, host participatory workshops to demonstrate the practical benefits Maintenance 4.0 offers. Create open forums where employees can voice their concerns and contribute ideas. This proactive approach strengthens their commitment to the transformation.
2. Balancing initial investment with long-term gains
The initial investment in Maintenance 4.0 can be significant, encompassing hardware, software, and training. The key is establishing clear, measurable objectives for return on investment (ROI).
Define success metrics early, such as downtime reductions or extended equipment lifespan. Tracking ROI with performance indicators (KPIs) will allow you to adapt your approach to achieve your goals.
3. Integrating new technologies without disrupting existing systems
Integrating Maintenance 4.0 requires merging new technologies with existing systems, which can lead to compatibility issues, especially with older equipment.
To facilitate integration, begin by assessing compatibility. Opt for modular solutions that adapt to your infrastructure’s needs, allowing each new technology to seamlessly blend with current processes. This approach helps avoid disruptions and enables gradual scaling.
4. Prioritising cybersecurity
In Maintenance 4.0, interconnected systems share data in real time, which increases the risk of cyberattacks. Prioritising cybersecurity is essential to protect both your data and networks.
Implement strong security policies, keep systems updated, and train staff in best practices for digital security. Investing in proactive monitoring tools helps prevent intrusions and safeguard data integrity.
5. Addressing skill gaps in the workforce
Maintenance 4.0 requires specific skills, including data analysis and IoT equipment management. Planning tailored training programmes for all employees is essential.
Create ongoing training pathways to help your teams gain the necessary skills for new technologies. Collaborating with experts or specialised training centres can also expedite skills development, ensuring your organisation fully leverages Maintenance 4.0’s potential.
6. Leveraging real-time data for strategic decision-making
Maintenance 4.0 systems generate extensive data, but their value lies in how well they’re analysed and applied. Leverage powerful analytical tools to turn this data into actionable insights.
Interactive dashboards enable real-time monitoring of equipment, allowing you to identify maintenance needs before issues arise. AI-based tools can further enhance fault prediction and optimise interventions, resulting in data-driven decisions that increase efficiency.
Optimising preventative maintenance with professional cleaning
Maintenance 4.0 is not only about advanced technologies. Consistent equipment upkeep is also essential for optimal performance. In industrial settings, professional cleaning can prevent issues by reducing dust and debris accumulation.
For specialised cleaning solutions, visit maintenance-40.com. Professional services ensure the longevity of your installations, strengthening Maintenance 4.0’s impact and preventing unnecessary downtime
Practical tips for a successful transition to maintenance 4.0
Here are additional strategies for ensuring a smooth, efficient transition to Maintenance 4.0.
Implement a gradual integration strategy
Create a transition roadmap, clearly defining priorities and identifying essential resources. This preventive approach reduces surprises and facilitates a smooth scale-up.
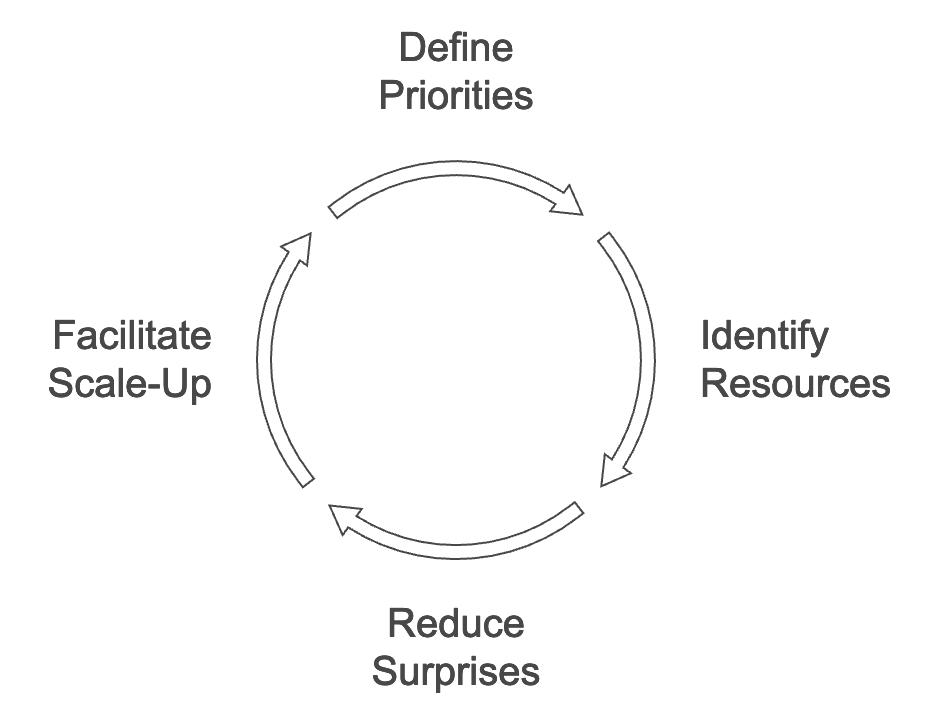
Measure impact and adjust as needed
For a successful transition, regularly review outcomes and adjust actions based on KPIs. This iterative approach allows you to refine your process to meet established goals.
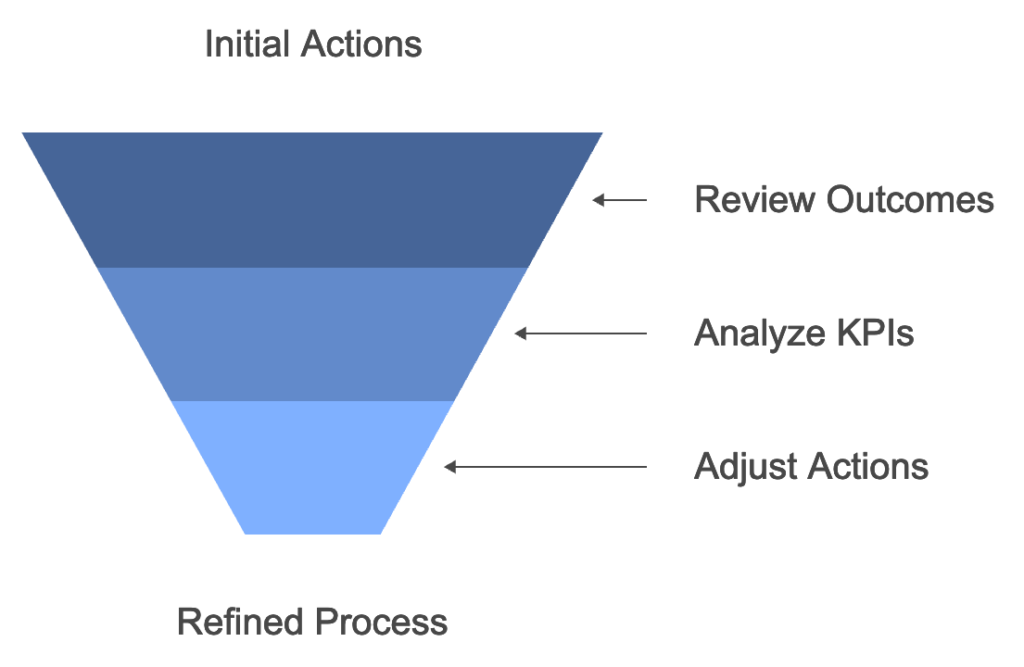
Work with expert partners
Working with Maintenance 4.0 experts can provide tailored advice and technical support. Partnering with trusted specialists offers access to their expertise, enabling a faster and more effective transformation.
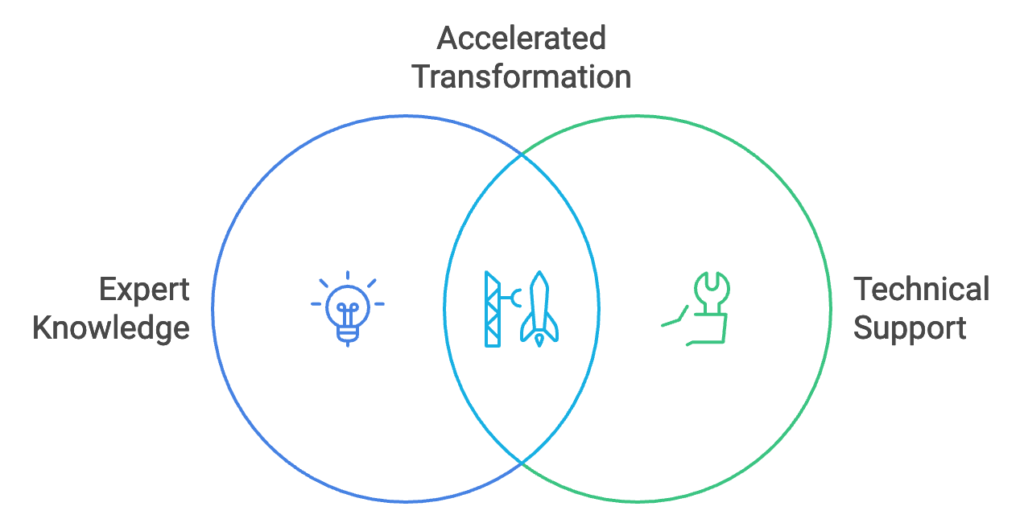
Conclusion
Transitioning to Maintenance 4.0 brings numerous advantages but demands a structured approach. By engaging teams, prioritising cybersecurity, and developing essential technical skills, you position your business to thrive in this technological shift. With careful planning and the right partners, Maintenance 4.0 becomes an opportunity to transform operations and remain competitive in a rapidly evolving industrial landscape.
No responses yet